UPM developed plastic conveyors with the side frames produced from High Molecular Weight Polyethylene (HMWPE). This was made to eliminate the need for belt tracking and tensioning.
The side frames are cut on an in-house router together with the machining of channels either side of the frames to locate the belt. This offers an ideal solution for changing the angle, or swan neck conveyor arrangements. Ensuring quick belt release for ease of clean down, achievable via manually operated tension release arms that operate via the top dead centre logic. This allows all aspects of the conveyor to be cleaned without the need for any special tools. Meaning this is a direct benefit to the operator in ease of maintaining a high care area, particularly for food applications.
UPM offer a free advisory service to their clients, resulting in a bespoke customer engineered solution, which then results in a Performance Guarantee. Allowing peace of mind with reliability and trouble free operation.
Twin Swan Neck Conveyor to Bagging Machine
Transporting multipacks of chocolate bars
- Food approved conveyor sides in HMWPE
- Food approved link belt with quick removal for cleaning
- 100mm high scooped flights
- Variable speed control and e/stop interfaced to bagging machine
- 304 Stainless steel support frame
Soft Fruit Tray Filling
Transporting trays at a rate of 100 per minute filling from a vertical twin head multi weigher machine
- 1000mm infeed to 1000mm discharge height
- Food approved link belt
- Quick belt removal for easy clean down
- Food approved conveyor sides in HMWPE
- Adjustable guide rails for various tray sizes
- 304 Stainless steel support frame
- Twin drive system each with an invert
- Sensors for stop / start during tray filling
Triple Decker for UPM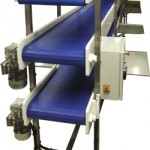
UPM Conveyors have established preferred supplier status to Finlays Fresh Produce who were the first suppliers of Fairtrade vegetables into the UK. Roger Broughton Group Engineering Manager states UPM were selected due to their ability to offer bespoke solutions to product handling in Kenya where trouble free operation and zero maintenance are priorities.
Finlay’s, established in 1750, has a substantial horticultural business which is involved in the growing, processing, packaging, marketing and distribution of cut flowers and premium prepared fresh produce, supplying several leading UK retailers. The company has major farming interests in Kenya, South Africa and China and is the largest vertically integrated added value horticultural producer and exporter of fresh produce and flowers from Africa to the EU. Finlays produced over 165 million packs of vegetables for the UK retail market in 2010 amounting to 29 million kilos of the freshest vegetables.